Gotham Brick & Tile Company Works.
|
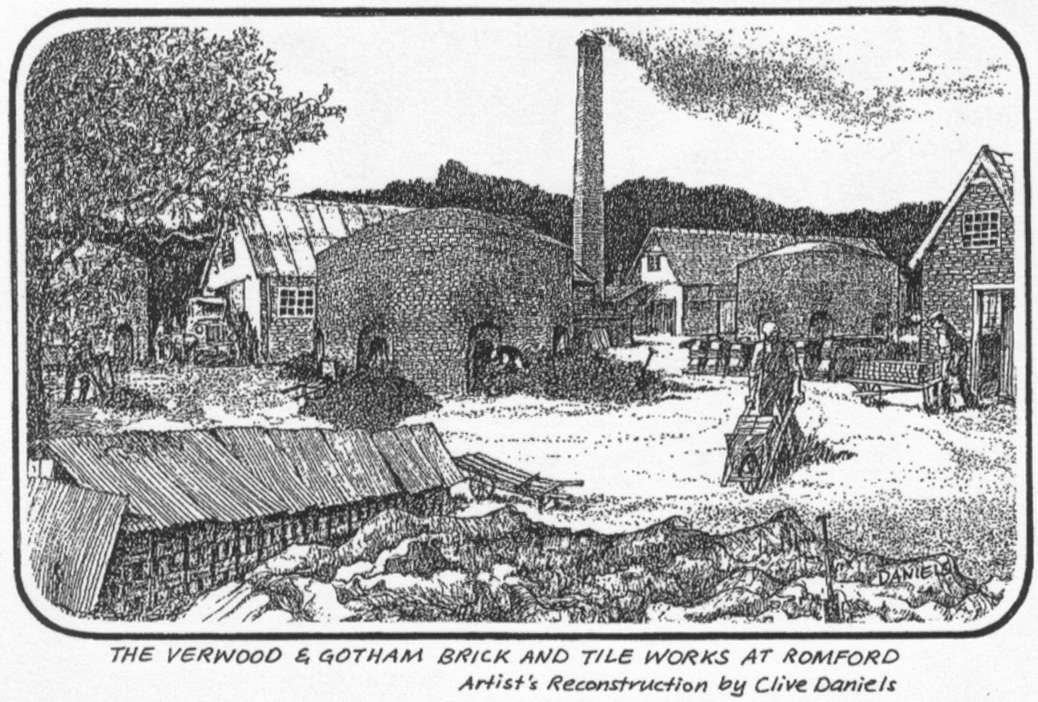
This
brick and tile yard was situated in Romford on the western
edge of Verwood in Dorset in the UK. It is now derelict and
it was fortunate to be able to see the kilns and chimney as
they were gradually demolished. It is a sad thing that all
evidence of a brickyard has virtually gone for ever.
Mr. Waters was the
only tile maker still living in the village in 1967. He came
with his father and brothers, a family of tile makers from
Sussex
to boost the output of tiles in Verwood. He was delighted
to talk of his work and could not resist illustrating his
memories.
Apparently
yellow and brown, clay was dug on the site, these clays
producing good red bricks. Three parts clay and
one part sand were mixed with water in the pug mill until
the mixture was like putty. It was left to stand for one
day. In the early days, bricks were made in a
mould by hand or in a presser which pressed out one brick at
a time. In later years a cutter which cut four housebricks
at a time was attached to the outlet of the pug mill, and I
understand that another attachment could be fitted for
making drain pipes. Fie-place bricks were also made.
The pug for tile making was made much softer
than that for bricks and was taken from the pug-mill in
large chunks to be made into tiles by hand. As Mr. Waters
said he "had to have a system" to make tiles
rapidly without wasted time and effort.
The picture shows the buildings
that housed the "pug-mill" and other brick making
equipment.
The
clay was placed on the right hand side of the work-bench, a
box of sand on the left and the tile mould, made of wood or
iron, placed on a piece of oak in the centre. When the mould
and base were sanded, a lump of clay was cut and thrown into
the mould the top being cut level with a wire
"bow". This surface was smoothed level with a
wooden striked dipped in water, which was used in two quick
strokes. The mould was then lifted off the tile
which was placed on the sanded floor. Mr. Waters
informed me that this method of tile making is the
Staffordshire method.
The
tiles were then dried on racks until they were leather hard
when they were bevelled on a "wooden horse". Five
tiles were placed on top of one another on the horse and the
wooden top was pressed on top of these. The
tiles were then stacked in piles of five on the drying shed
floor until bone dry, this stage was called
"checkering". The tiles were then
fired at the same time as the bricks.
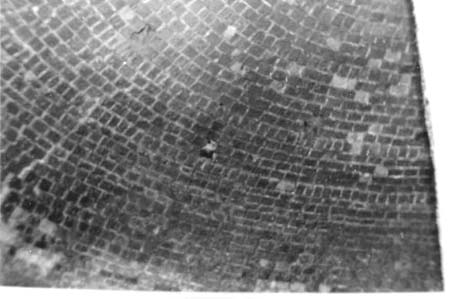
"The pictures show the
Belgium Kiln, Exterior and Interior."
The
kilns used during Mr. Waters' time were circular Belgian
type kilns with firing holes at intervals all round and one
entrance used when stacking and removing bricks and
tiles. Apparently before 1924 square Scotch
kilns were used. These were twelve feet high with six firing
holes along each side and an entrance hatch at each end. By
the descriptions
I
have heard they had no roof, the top bricks were watched
during the firing to judge the heat obtained. These top
bricks the "plotters'' also kept the heat in.
The pictures shows the remains of a Skotch
kiln.
The bricks were
stacked in the bottom and at the sides of the kiln and the
tiles stacked within them. As Mr. Waters
explained, the tiles were stacked on their bottom edges so
that the lip at the top kept the tiles apart, allowing the
heat to travel between them. The firing with coal, took two
days and nights the fires being checked every two hours. The
draught was drawn up from the firing holes and then down
through a central pillar in the kiln, under the drying
sheds, through flues and up through an eighty feet high
chimney. During the firing "the bricks
became nearly white hot".
The
entrance hatch was bricked up during firing, but one brick
was left loose so that three half-tiles which had been
placed in a certain position could be pulled out with a
hooked iron rod for testing. When firing was complete the
kiln was left to cool.
Most
of the tiles were a "natural red", others were
coloured, the colouring being mixed with sand used at the
moulding stage. Manganese with sand produced black tiles;
manganese alone gave a purple colouring and a mottled effect
was obtained by sprinkling manganese over the tiles after
they had been sanded. When green tiles were
required, the tile makers had to tour the nearby fields
collecting fresh cow-manure. This was made into a solution
with water and manganese and was painted onto the surface of
the tiles.
A
variety of different shaped tiles were made including the
normal tiles, one and a half tiles, half tiles or slips,
eave, ridge, hip and valley tiles as well as decorative,
wall tiles.
Until
1910 the bricks and tiles were taken to the surrounding
villager, and towns by horse and cart, the number of bricks
per load depending on the size arid ability of the
horse. Some horses could pull as many as three
hundred and fifty to four hundred bricks. After 1910 the
bricks were
transported by Foden's steam lorries and could be taken
greater distances. I understand that the' roof of
Bournemouth Pavilion is tiled with Verwood tiles.
Mr.
Waters said that he made an average, of four thousand tiles
per week for which he was paid thirty two shillings. He was
reminded by his wife that he always worked on Sunday
mornings, for which he was paid no extra. He and his family
made tiles in Verwood for fifty years, until the outbreak of
the second world war.
Mr-
Waters - a craftsman at heart - enjoyed inventing in his
spare time and made some beautiful model ships from rough
wood and "odds and ends" as he called them.
Copyright © P Reeks.
|